Closed Cell Elastomeric Foam : Getting to understand it.
Closed cell elastomeric foam is a synthetic rubber with a vapor barrier surface (skin) and made of closed cell structures (pockets).
Pocket Protection in Football and Foam
In football, the success of the quarterback is most typically attributed to the protection he gets while standing in the pocket. The offensive linemen build a wall around the quarterback to prevent him from being sacked, and, pushes back against the pressure of the defense.
Now, in the world of foam, the offensive line is the “closed cell”. Closed cell refers to rubber-like properties of a polymer which demonstrate an ability to regain original form after being compressed.
Using scientific terms this capability is known as “compression deflection”. A typical standard used to measure compression deflection for cellular rubber materials is ASTM D1056.
An added benefit to closed cell construction are the completely sealed “pockets” which [unlike sweaty offensive linemen] do not exchange gases with one another.
Benefits of Closed Cell Construction
Since these “pockets” are completely sealed they are said to have a “closed cell” construction.
Each closed cell tends to have lower water, gas, and oil absorption than open cell pockets.
These factors allow closed cells to be stiffer, or more rigid.
Similar to defensive schemes in football, the closed cell can be constructed in difference ways. This is done by altering its density, rigidity, compression resistance, and other attributes.
We will discuss how these interior “pockets” of protection are formed later on when we explain the manufacturing process.
For now, let us turn our attention to the outer construction of closed cell elastomeric foam.
Vapor Retardant Skin of Elastomeric Foam
Elastomeric foam has a smooth surface called a “skin”. The skin runs along the outside edge and acts as a built-in vapor retarder, not a vapor barrier.
Here is the difference.
In construction, a vapor barrier is any material used for damp proofing. Most typically a plastic or foil sheet, that resists diffusion of moisture through the wall, floor, ceiling, or roof assemblies of buildings. The vapor barrier is used to prevent interior condensation of whatever it is wrapped around.
In manufacturing, a vapor retarder is a material that reduces the rate at which water vapor can move through a material.
Some manufacturers use the term “vapor barrier” even though “vapor retarder” is more accurate.
When measuring the ability of a material to retard the diffusion of water vapor one uses units known as “perms” or permeability.
You will find the “skin” of elastomeric foam to be less vulnerable to cracks, breakage, and material loss due to its elastic and flexible nature.
Building the Perfect Foam for Your Application.
Now that you understand the properties of a closed cell, skin, and their combined benefits, you can see many useful ways to utilize closed cell elastomeric foam.
Closed cell elastomeric foam is ideal for use in damp applications such as gasketing and insulation. It is offered in tubes, sheets, or rolls from a factory.
Using our product search tool you can compare closed cell elastomeric foam to other material choices.
If you are interested in knowing more about closed cell elastomeric foam, and whether it is an ideal fit for your application, contact Worldwide Foam today. You can also call the office at (574) 968-8268.
Should you have other questions and do not wish to speak with a human yet, please check-out our FAQ page.
If you are enjoying this reading, we encourage you to keep going.
Next, we will discuss the manufacturing process of closed cell elastomeric foam.
How Closed Cell Elastomeric Foam is Made
Every time you bake something you need to have a recipe.
The recipe tells us how much of each ingredient to use, as well as, the duration and temperatures at which to bake.
The recipe for Elastomeric Foam consists of these ingredients:
- Synthetic rubber blend, typically nitrile butadiene rubber (NBR) and/or ethylene-propylene-diene monomer (EPDM)
- Polyvinyl chloride (PVC)
- A chemical foaming agent
A mixture of these materials is put through extruding equipment to form a particular profile or shape.
This is similar to using a bunt to bake a cake with a hole in the middle.
The most common shapes used in baking foam are a continuous roll or a flat sheet.
Next, it is heated in an oven to a specific high temperature. The high temperature stimulates the foaming agent and converts it from solid to gas.
Earlier we promised to discuss how “pockets” are made. While the foaming agent converts from solid to gas thousands of small and inter-connected air pockets are formed. These air pockets are called “closed cells”. Additionally proprietary methods are used to form and shape the skin. Voila. You have bake foam, but, please do not try to eat it. Yuck!
Where to Buy Closed Cell Elastomeric Foam?
The closed cell elastomeric foams offered by Worldwide Foam are extremely durable. They are made without the use of chlorofluorocarbons (CFCs), hydrochlorofluorocarbons (HCFCs), or hydrofluorocarbons (HFCs). As a result, they are suitable for the toughest environmental specifications.
Contact Worldwide Foam to learn more about elastomeric foam and its applications?

Elastomeric Foam Types
- Nitrile Butadine Rubber (NBR)
- Ethylene Propylene Diene Monomer (EPDM)
- Chloroprene (CR)
- Epichlorohydrin (ECH)
- Styrene-butadiene rubber (SBR)
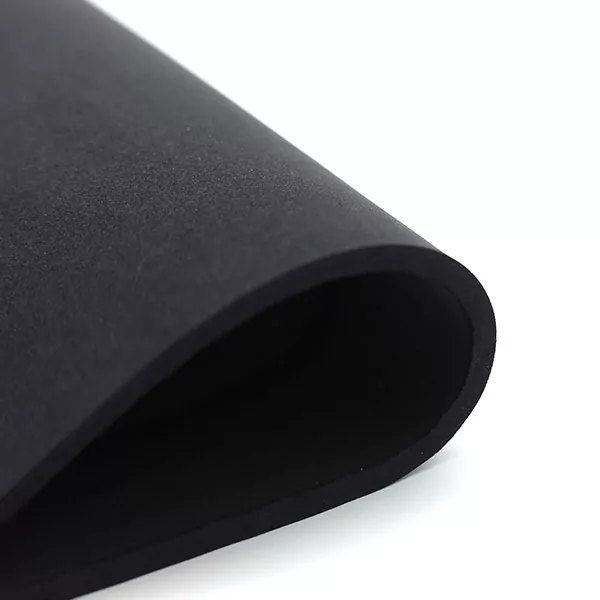



Common Application and Markets Served
For many year, closed cell elastomeric foam has been widely used in various industrial and consumer applications. Here’s a brief list of some common applications and industries our customers use this material for:
- Automotive gaskets and sealings
- Aerospace
- HVAC components and insulations
- Flexographic printing
- Appliances
- Electronics and enclosures

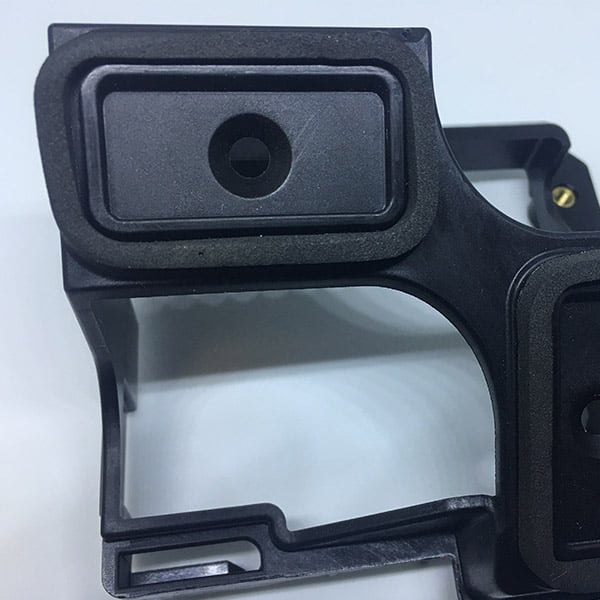


How to select the right materials?
The material selection process could be tricky and there are many aspects and requirements involved. We, as a material supplier, carry a wide array of products across many manufacturers. We carry Armacell, K-Flex, INOAC, WM T. Burnett, and Hutchinson, to name a few. Our materials selection guide is a great tool to start and narrow down your selections based on applications, fire retardant rating, oil/fuel resistance rating, and UV resistance. Our informative product specialists could assist you and answer any product-related questions you may have!
Why Worldwide Foam?
Since 2008, Worldwide Foam has been revolutionizing the industry. We offer one-day lead time from our seven strategic locations. We provide the widest ranges of closed cell cross-linked polyethylene foam and elastomeric foam in the industry. We are constantly expanding our servicing capabilities to supply you the best options for your press-ready goods.
Worldwide Foam always has the customer in mind by providing add-on services that save our customers time and money. Convenient services such as our heat lamination, skiving and f&k looper allow customers to get press-ready goods fast! And, with our 8 million board foot inventory, we are sure to have material for any project.